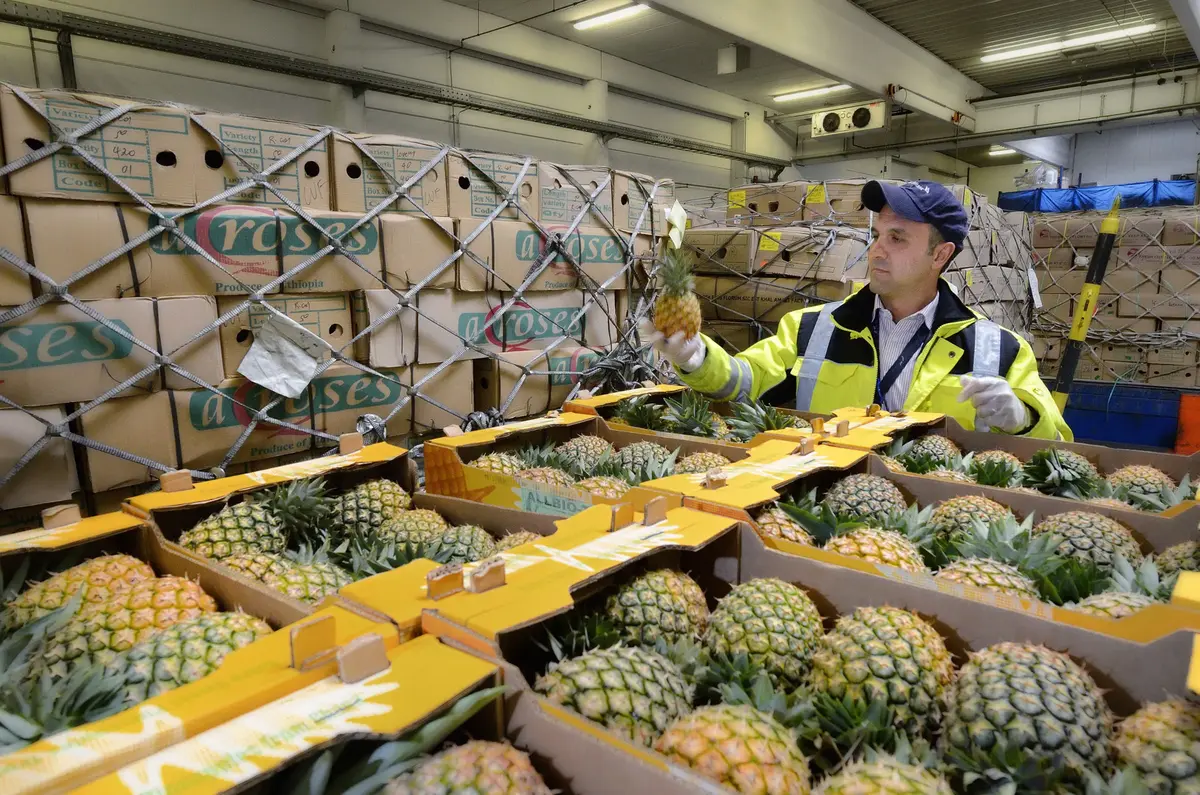
Elevating Excellence: Quality Control in Air Freight Operations
In the fast-paced world of air freight operations, ensuring the highest quality standards is paramount. Quality control serves as the backbone of successful air freight management, safeguarding against errors, delays, and potential mishaps. Let’s delve into the intricacies of quality control in the air freight industry and explore how it plays a pivotal role in elevating excellence.
Defining Quality Control in Air Freight Operations
Quality control, in the context of air freight operations, refers to the systematic processes and measures implemented to guarantee that each stage of the freight journey adheres to predetermined standards. These standards encompass various aspects, including safety, compliance, and efficiency.
The Significance of Quality Control in Air Freight
The importance of quality control cannot be overstated. In an industry where time sensitivity and precision are non-negotiable, effective quality control safeguards against potential disruptions and ensures a smooth and reliable freight experience. Now, let’s dissect the key components that constitute a robust quality control framework.
Key Components of Quality Control
Inspection and Testing
One of the foundational pillars of quality control is rigorous inspection and testing protocols. From the moment a shipment is received to its final delivery, each step undergoes meticulous scrutiny to identify any deviations from the established standards.
Documentation and Record-Keeping
Accurate and comprehensive documentation is essential for traceability and accountability. Quality control involves maintaining meticulous records of each shipment, facilitating transparency and aiding in the swift resolution of any discrepancies.
Compliance with Regulations
Adherence to international and local regulations is non-negotiable in air freight. Quality control ensures that every aspect of the operation complies with the ever-evolving legal landscape, mitigating the risk of legal complications.
Technology’s Role in Quality Control
In the era of digital transformation, technology plays a pivotal role in enhancing quality control measures within air freight operations.
Automation in Freight Operations
Automated systems streamline processes, reducing the likelihood of errors caused by manual intervention. From sorting packages to managing inventory, automation contributes significantly to operational efficiency.
Tracking and Monitoring Systems
Real-time tracking and monitoring systems provide unparalleled visibility into the freight journey. This not only enhances security but also enables proactive problem-solving in the event of deviations from the planned route or schedule.
Data Analysis for Continuous Improvement
Harnessing the power of data analytics allows for continuous improvement. By analyzing performance metrics, air freight companies can identify trends, address recurring issues, and optimize their operations for maximum efficiency.
Challenges in Quality Control
Despite the advancements in technology and meticulous planning, challenges in quality control persist.
External Factors
External factors, such as adverse weather conditions or customs delays, pose a constant challenge. Quality control measures must be flexible enough to accommodate unforeseen circumstances.
Communication and Coordination Issues
Effective communication and coordination among various stakeholders, including airlines, ground handlers, and customs authorities, are essential. Breakdowns in communication can lead to errors and delays.
Human Error
As with any industry, human error remains a potential pitfall. Quality control strategies must account for the possibility of mistakes and implement safeguards to minimize their impact.
Strategies for Effective Quality Control
Addressing the challenges requires proactive strategies that go beyond technology.
Training and Skill Development
Investing in the training and skill development of personnel is crucial. Well-trained staff are better equipped to handle unexpected challenges and adhere to established protocols.
Collaboration and Communication Enhancement
Facilitating seamless collaboration and communication between all parties involved fosters a cohesive and efficient operation. Regular training sessions and joint exercises can enhance coordination.
Implementing Robust Standard Operating Procedures (SOPs)
Establishing and consistently enforcing robust standard operating procedures ensures a standardized approach to quality control. This reduces the likelihood of errors caused by variations in processes.
Benefits of Implementing Quality Control
The rewards of a well-implemented quality control system extend beyond operational efficiency.
Enhanced Customer Satisfaction
Reliable and error-free air freight operations contribute to enhanced customer satisfaction. Meeting or exceeding delivery expectations builds trust and loyalty.
Cost Savings and Efficiency Gains
By minimizing errors and delays, quality control measures contribute to cost savings and operational efficiency. Streamlined processes result in a more economical freight operation.
Reputation Management
A reputation for reliability and quality can be a significant differentiator in the competitive air freight industry. Consistent adherence to high standards enhances the company’s standing in the market.
Conclusion
In conclusion, elevating excellence in air freight operations requires a holistic approach to quality control. By embracing technological advancements, addressing challenges, implementing effective strategies, and learning from both successes and failures, the industry can ensure a future marked by reliability, efficiency, and customer satisfaction.
Frequently Asked Questions (FAQs)
Q: How can air freight companies mitigate the impact of external factors on quality control?
A: Air freight companies can develop contingency plans, leverage technology for real-time monitoring, and maintain open communication with all stakeholders.
Q: What role does training play in ensuring quality control in air freight operations?
A: Training is essential for equipping staff with the skills and knowledge needed to adhere to quality control standards, reducing the likelihood of errors.
Q: What are the long-term benefits of implementing sustainable practices in air freight operations?
A: Long-term benefits include cost savings, improved environmental impact, and a positive brand image in an increasingly eco-conscious market.
Q: How can small and medium-sized air freight companies compete with larger counterparts in terms of quality control?
A: Small and medium-sized companies can focus on niche markets, invest in technology, and prioritize customer satisfaction to compete effectively.